Installing Your Infield Skin
KEYS TO ENSURING SUCCESS
Choosing the right infield soil for your ballfield is just half the battle, making sure it is installed correctly is equally important. There have been plenty of examples where quality infield materials fail to perform only to find out the product was installed incorrectly, crippling its future success. There can be several reasons for failed infields, not the least of which is choosing the wrong infield material. The following keys should be closely monitored once a project is underway.
Detailed specifications cannot be understated.
If your ballfield is part of a larger project, then you’ll likely have a spec book created for the project that provides all of the guidelines for contractors. There is a direct correlation between the clarity of the installation instructions and the success of your infield installation. The more vague the specifications, the more that’s left to the contractor. Therein lies the problem. Typically, most infield specs provide little or no instruction for proper installation. An infield material is only as good as its installation. Learning that lesson early on, DuraEdge spells out precise, detailed instructions. But, as the customer it is on you to properly vet potential installers. You should require a strict set of qualifications for anyone bidding to build or renovate your infield. DuraEdge maintains a list of “preferred installers” who have been properly vetted and can ensure the correct installation equipment and procedures are followed. Remember, if an installation fails, it is difficult to assign responsibility for what happened if your project did not start with detailed installation instructions and specifications.
- Prepping the subgrade.
While you may be zeroed in on how your finished infield will look, the subgrade beneath your infield is equally important. It should have a slope that replicates what the finish grade will be. This is critical to ensure a consistent depth of infield material across the entire plane of the infield skin. If the subgrade is inconsistent, the depth of your material will vary and that will result in inconsistent performance of the infield skin. - Surface finish grade and a consistent slope.
In other parts of this guide we talked about how important the surface finish grade is. No infield material — no matter how good it is — will work well if there are issues with the flow of water across it. If water has the ability to sit on an infield, it will soften that infield. The surface grade of the infield must have a consistent slope from one side to the other to keep water moving. The groundskeeper’s job is to maintain proper surface grade over time. Modern construction equipment utilizes lasers to guide or operate the grading equipment for laying down the most precise grade, which is to be within a tolerance of ± 1/8″. This must be accomplished for a successful installation, so be sure you find experienced field installers with the proper equipment to do the job right. This is definitely not the part of the project where you can take a shortcut or bring in your neighbor who says he has a skid steer and will do it for free. You only get funding once, do it right the first time. - Compaction of both subgrade and infield material.
Compaction involves removing pore space in a soil which increases soil density and soil firmness. Compaction is important not only for the infield material, but for the subgrade layer beneath it as well. Maximum density/firmness are determined by the makeup of the soil including the percentage of sand, silt, clay, and organic matter present, as well as the mineralogy of the soil. DuraEdge calls for their infield soil material to be optimally compacted to 85-90% as achieved on a standard “Proctor” test (see below). To accomplish this, the subgrade must be compacted to at least 90% Proctor or higher. If compaction is less than 90%, the infield material above it will struggle or even fail to achieve the required compaction which can result in a faulty installation and poor infield performance. If the existing subsoil is not able to achieve 90% compaction, remove subsoil and replace with a granular fill of a 3/8″ minus angular stone product and compact. For the infield soil, a 4″ profile should be installed and compacted in layers up to 2″ thick to ensure necessary compaction throughout the profile. These layers are called “lifts”.
The Proctor compaction test is a laboratory method of experimentally determining the optimal moisture content at which a given soil type will become its most dense and achieve its maximum dry density (compaction). - Don’t forget to add the “glue” — also known as water.
One of the key components for proper compaction of soil is moisture. It is truly the “glue” that holds soil together. Water and scarification help the compressed soil to bind and hold, which removes pore space. If an infield soil is left too dry when the installer attempts to compact, the soil simply will not bind. The negative consequence of unbound soil will be apparent with the first rain event on the new infield. It will quickly turn into a quagmire. Inadequate compaction during installation due to a lack of moisture allows the pore space to remain, which then fills with rainwater. To prevent this scenario, during installation think, “Moisten. Scarify. Add. Compact.” When you’re adding a new lift of soil, be sure to moisten the soil that you are adding to, then scarify that surface before adding the next lift and compacting with a roller. The one caveat is to not over water the soil. The goal is enough water to permeate through the entire soil layer, but not so much that it becomes saturated, fills all the pore space and pumps when attempting to compact due to too much soil moisture.
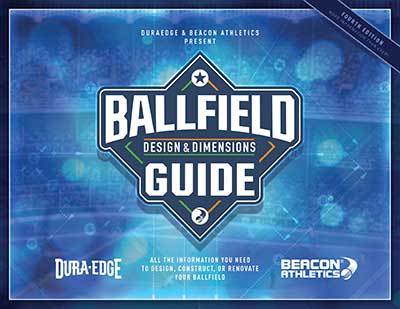